Trouble in the system: Is it the pump, blower, or furnace?
It’s Monday morning and you can’t pump your workhorse furnace below 40 millitorr. You have helium leak-checked the most obvious spots and there are no leak indications. You have bled in a “puff” of helium into the mechanical pump gas ballast valve port to verify that you are able to see helium. This sort of clears the helium blower and mechanical pump. Your hunch is an internal water leak and the 40 millitorr you are seeing is the vapor pressure of the ice formed by the leak. Before blowing down the water from the internal heat exchangers and furnace shell (a big messy time-consuming job!), you need to know if all that trouble is warranted.
Isolate the Pumps
The next step is to blank off the blower inlet and verify a vacuum level below 10 millitorr (blower running) test point B. Note that with the blower at rest and the mechanical pump running, you will normally see 500-1000 millitorr at the inlet since you are pumping dirty roughing piping with high outgas loads through the low conductance internal clearances of the blower at rest.
If the blank off is done by closing the roughing valve, you might have high blower inlet vacuum due to a seat leak on the roughing valve. To verify, helium needs to be sprayed into the valve seat/disc area but in most cases, this cannot be done due to piping placement, etc. The fix is to drill a hole in the roughing piping near the roughing valve and TIG weld in an “O” ring sealed test port. (We make a mild steel port with an SAE “O” ring sealed plug for this purpose). This allows easy helium access to the valve seat (with the rough valve closed), and a leak-tight seal with the piping under operating conditions.
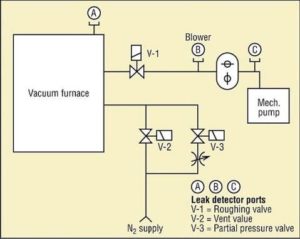
If the rough valve seat is tight and the blower inlet still at the 40 millitorr or so level, the mechanical pump base vacuum needs checking. It is possible there could be a high water or solvent load in the mechanical pump oil causing high blank off in the 500- 1000 millitorr range. Since previous leak checking showed the blower and interconnecting piping to be tight, with no seal leaks on the roughing pump, the problem must lie in the pump. If the pump oil is “milky” due to water absorption, it is possible to gas ballast it away and several oil changes might be needed to get the rough pump base vacuum down to under 50 millitorr. We have seen high blank offs with clear pump oil that had weird organic volatiles in it, so clear oil in itself does not mean a low base vacuum. We have also seen water leaks in the internal heat exchangers but with clear mechanical pump oil!
Digging Deeper
Next to check are the vent and partial pressure valves. The argument on the roughing valves still applies here. You need to introduce helium on the upstream side of the valves (with them closed). The problem 2 is most venting is done with nitrogen/ argon at 30-60 psi. This needs to be valved off and suitable piping changes made to allow helium to be bled in. The partial pressure valves are more easily checked since the piping is of smaller diameter and easier to disconnect or valve off.
If not previously leak checked, remove the electrical junction box on the recirculating fan motor (if equipped) and probe the three-phase power feedthroughs and motor internal temperature switch feedthroughs. IMPORTANT: check voltage on the power leads with a DVM before probing!
Certain air cylinders pose another problem if the vacuum seal on the rod is provided by the seal package on the nose of the air cylinder. This is the construction we have seen on an old vacuum oil quench furnace. Leak checking this construction means disconnecting the air line to the bottom cylinder port and applying helium.
Finally, if there are vacuum/pressure switches piped into the furnace chamber, they need their covers removed and helium introduced to verify no diaphragm leaks. At this point, you can be fairly certain that the problem is ice in the furnace. This can arise from water leaks on the internal heat exchangers (more common)or a hole in the furnace shell caused by corrosion of the water jacket ( a rare occurrence). Testing the heat exchangers will involve blowing out the water with compressed air, waiting several hours for the ice to melt, and with the leak detector valved in, bleeding in a slug of helium into the water line. Testing the furnace shell involves draining the shell (a big undertaking) and flowing helium into the water jacket.
Some Other Techniques
Another good method to locate water leaks is to add fluorescent dye into the process water system. Leaks can then be pinpointed using a “black light” source. If the heat exchanger is internal and to the rear of the furnace, the hot zone would have to be removed to gain access. Blacklight testing on the furnace shell and door would be fairly easy.
All this can be eliminated if a residual gas analyzer (RGA) is available and connected to the furnace! A high water peak would point the way to an internal heat exchanger or furnace shell/door leak while a high nitrogen peak would mean looking at the vent and partial pressure valving. A decent RGA system probably costs in the $30,000 range and makes sense for multiple furnace installations handling costly aerospace parts.
— Geoff Humberstone